SMT از تحلیل و راه حل حفره جوشکاری جریان هوا خمیر لحیم معمولی استفاده می کند (نسخه Essence 2023)، شما شایسته آن هستید!
1 مقدمه

در مجموعه برد مدار ابتدا خمیر لحیم روی لحیم صفحه مدار چاپ می شود و سپس قطعات مختلف الکترونیکی چسبانده می شود. در نهایت، پس از کوره جریان مجدد، دانههای قلع موجود در خمیر لحیم کاری ذوب شده و انواع قطعات الکترونیکی و لحیم کاری برد مدار به یکدیگر جوش داده میشوند تا مونتاژ زیرماژولهای الکتریکی محقق شود. تکنولوژی سطحی (sMT) به طور فزایندهای در محصولات بستهبندی با چگالی بالا، مانند بستههای سطح سیستم (siP)، دستگاههای ballgridarray (BGA) و تراشه برهنه قدرت، بسته بدون پین مسطح مربعی (quad aatNo-lead، به نام QFN) استفاده میشود. ) دستگاه.
با توجه به ویژگی های فرآیند جوشکاری خمیر لحیم کاری و مواد، پس از جوشکاری جریانی این دستگاه های سطح لحیم کاری بزرگ، سوراخ هایی در ناحیه جوش لحیم ایجاد می شود که بر روی خواص الکتریکی، خواص حرارتی و خواص مکانیکی محصول تاثیر می گذارد و عملکرد آن را تحت تاثیر قرار می دهد. حتی منجر به خرابی محصول می شود، بنابراین برای بهبود حفره جوشکاری مجدد خمیر لحیم کاری به یک فرآیند و مشکل فنی تبدیل شده است که باید حل شود، برخی از محققین علل ایجاد حفره جوش گلوله لحیم کاری BGA را مورد تجزیه و تحلیل و بررسی قرار داده و راه حل های بهبود لحیم کاری معمولی ارائه کرده اند. مساحت جوشکاری فرآیند جوشکاری مجدد خمیری QFN بیشتر از 10 میلیمتر مربع یا ناحیه جوشکاری بیشتر از 6 میلیمتر مربع محلول تراشه لخت وجود ندارد.
برای بهبود سوراخ جوش از جوشکاری پیش فرم لحیم کاری و کوره رفلاکس خلاء استفاده کنید. لحیم کاری پیش ساخته برای نقطه شار به تجهیزات خاصی نیاز دارد. به عنوان مثال، تراشه پس از اینکه تراشه مستقیماً روی لحیم کاری پیش ساخته قرار گرفت، به طور جدی متحرک شده و کج می شود. اگر تراشه مانت فلاکس مجدداً جریان یابد و سپس نقطه باشد، روند دو بار جریان مجدد افزایش می یابد و هزینه لحیم کاری پیش ساخته و مواد شار بسیار بیشتر از خمیر لحیم است.
تجهیزات رفلاکس خلاء گران تر است، ظرفیت خلاء محفظه خلاء مستقل بسیار کم است، عملکرد هزینه بالا نیست و مشکل پاشش قلع جدی است که عامل مهمی در استفاده از چگالی بالا و گام کوچک است. محصولات در این مقاله، بر اساس فرآیند معمولی جوشکاری جریان مجدد خمیر لحیم کاری، یک فرآیند جدید جوشکاری با جریان ثانویه برای بهبود حفره جوش و حل مشکلات اتصال و ترک خوردگی مهر و موم پلاستیک ناشی از حفره جوش توسعه و معرفی شده است.
2 حفره جوشکاری و مکانیسم تولید چاپ خمیر لحیم کاری
2.1 حفره جوش
پس از جوشکاری جریان مجدد، محصول تحت اشعه ایکس آزمایش شد. همانطور که در شکل 1 نشان داده شده است، سوراخ های ناحیه جوش با رنگ روشن تر به دلیل لحیم ناکافی در لایه جوش است.
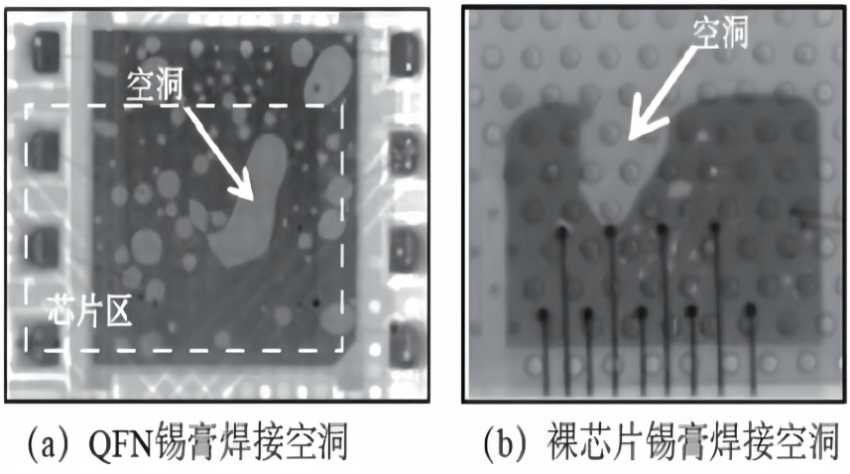
تشخیص سوراخ حباب با اشعه ایکس
2.2 مکانیسم تشکیل حفره جوش
با در نظر گرفتن خمیر لحیم sAC305 به عنوان مثال، ترکیب و عملکرد اصلی در جدول 1 نشان داده شده است. دانه های شار و قلع به شکل خمیری به هم چسبیده اند. نسبت وزن لحیم قلع به شار حدود 9:1 و نسبت حجم آن حدود 1:1 است.
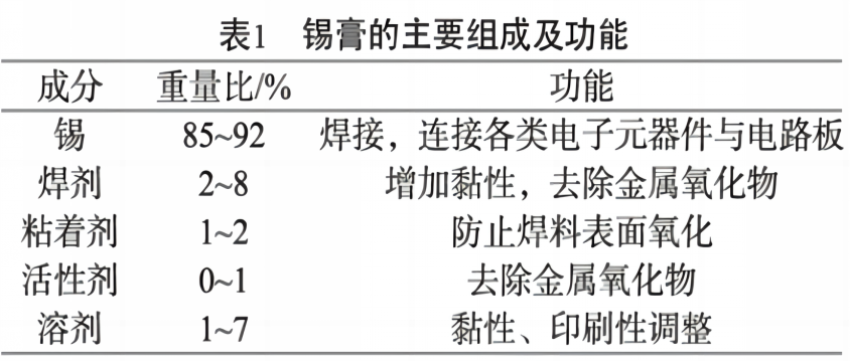
پس از چاپ و نصب خمیر لحیم با اجزای مختلف الکترونیکی، خمیر لحیم کاری با عبور از کوره رفلاکس چهار مرحله پیش گرم کردن، فعال سازی، رفلاکس و خنک شدن را پشت سر می گذارد. وضعیت خمیر لحیم کاری نیز با دماهای مختلف در مراحل مختلف متفاوت است، همانطور که در شکل 2 نشان داده شده است.
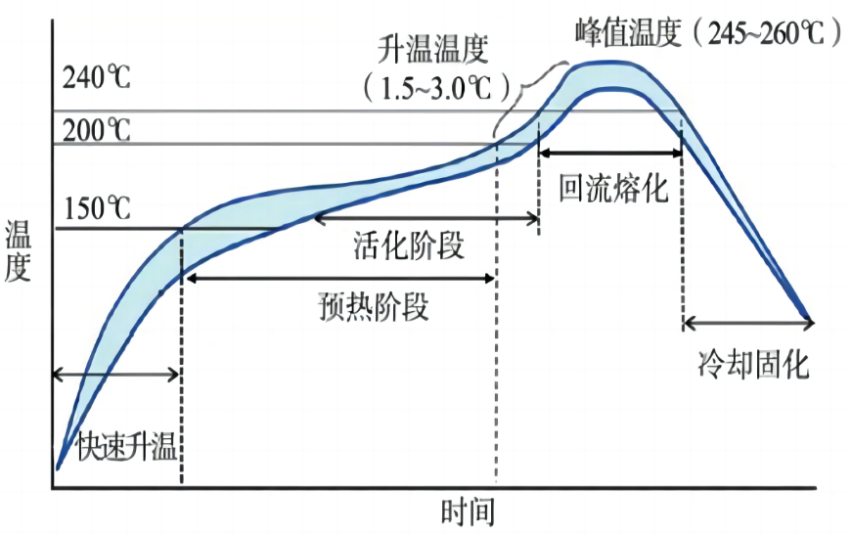
مرجع مشخصات برای هر ناحیه از لحیم کاری مجدد
در مرحله پیش گرم کردن و فعال سازی، اجزای فرار موجود در شار در خمیر لحیم کاری هنگام گرم شدن به گاز تبدیل می شوند. در عین حال، با حذف اکسید روی سطح لایه جوش، گازهایی تولید خواهد شد. برخی از این گازها تبخیر می شوند و از خمیر لحیم خارج می شوند و دانه های لحیم به دلیل تبخیر شدن شار به شدت متراکم می شوند. در مرحله رفلاکس، شار باقیمانده در خمیر لحیم به سرعت تبخیر میشود، دانههای قلع ذوب میشوند، مقدار کمی از گاز فرار شار و بیشتر هوای بین دانههای قلع به موقع پراکنده نمیشوند و باقیمانده در قلع مذاب و تحت کشش قلع مذاب ساختار ساندویچی همبرگر هستند و توسط لحیم کاری تخته مدار و اجزای الکترونیکی گیر میکنند و گاز پیچیده شده در قلع مایع تنها با شناوری رو به بالا به سختی از آن خارج میشود. زمان ذوب بالایی بسیار است. کوتاه هنگامی که قلع مذاب سرد می شود و تبدیل به قلع جامد می شود، منافذ در لایه جوش ظاهر می شود و سوراخ های لحیم ایجاد می شود، همانطور که در شکل 3 نشان داده شده است.
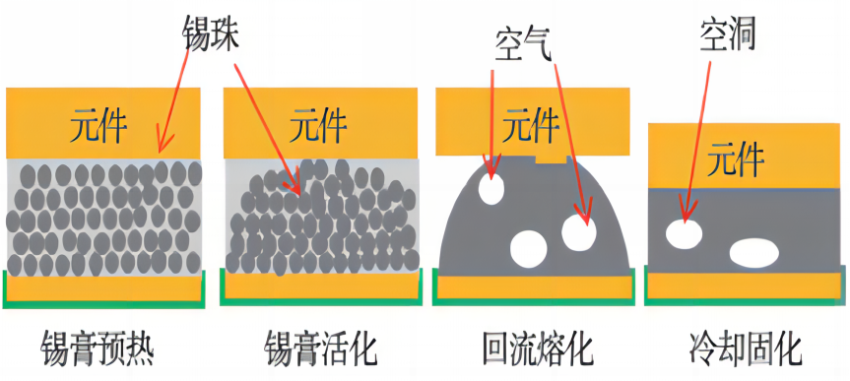
نمودار شماتیک فضای خالی ایجاد شده توسط جوشکاری مجدد خمیر لحیم کاری
علت اصلی ایجاد حفره جوش این است که هوا یا گاز فرار پیچیده شده در خمیر لحیم پس از ذوب به طور کامل تخلیه نمی شود. عوامل تأثیرگذار شامل مواد خمیر لحیم کاری، شکل چاپ خمیر لحیم کاری، میزان چاپ خمیر لحیم کاری، دمای رفلاکس، زمان رفلکس، اندازه جوش، ساختار و غیره است.
3. بررسی عوامل موثر بر سوراخ های جوشکاری جریان چاپ خمیر لحیم کاری
تستهای QFN و تراشههای لخت برای تأیید دلایل اصلی حفرههای جوشکاری جریان مجدد، و یافتن راههایی برای بهبود فضای خالی جوشکاری جریان مجدد چاپ شده توسط خمیر لحیم استفاده شد. مشخصات محصول جوشکاری جریان مجدد خمیر لحیم کاری QFN و تراشه لحیم کاری در شکل 4 نشان داده شده است، اندازه سطح جوش QFN 4.4mmx4.1mm است، سطح جوش لایه قلع شده (قلع خالص 100٪) است. اندازه جوش تراشه لخت 3.0mmx2.3mm است، لایه جوشکاری از لایه دو فلزی نیکل-وانادیوم پراکنده شده و لایه سطحی وانادیوم است. پد جوش زیرلایه الکترولس نیکل پالادیوم طلا فرو بردن، و ضخامت 0.4μm / 0.06μm / 0.04μm بود. از خمیر لحیم کاری SAC305 استفاده می شود، تجهیزات چاپ خمیر لحیم کاری DEK Horizon APix، تجهیزات کوره رفلاکس BTUPyramax150N و تجهیزات اشعه ایکس DAGExD7500VR می باشد.
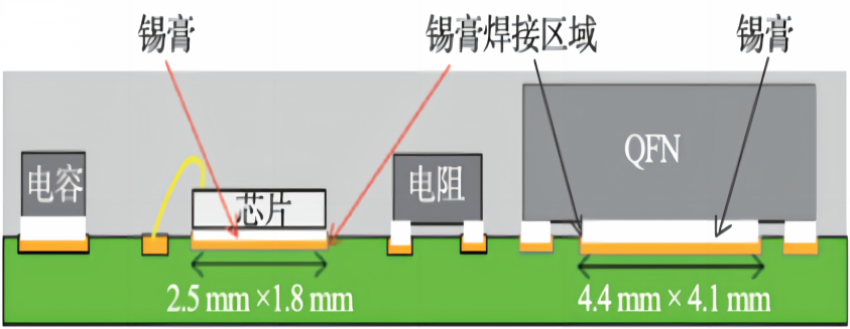
نقشه های جوشکاری QFN و برهنه
برای تسهیل مقایسه نتایج آزمایش، جوشکاری جریانی تحت شرایط جدول 2 انجام شد.
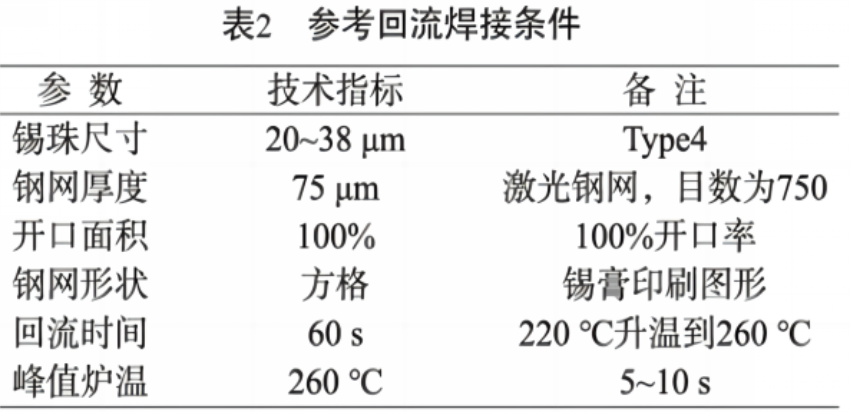
جدول شرایط جوشکاری Reflow
پس از اتمام نصب روی سطح و جوشکاری مجدد، لایه جوش توسط اشعه ایکس شناسایی شد و مشخص شد که سوراخ های بزرگی در لایه جوش در پایین QFN و تراشه لخت وجود دارد، همانطور که در شکل 5 نشان داده شده است.
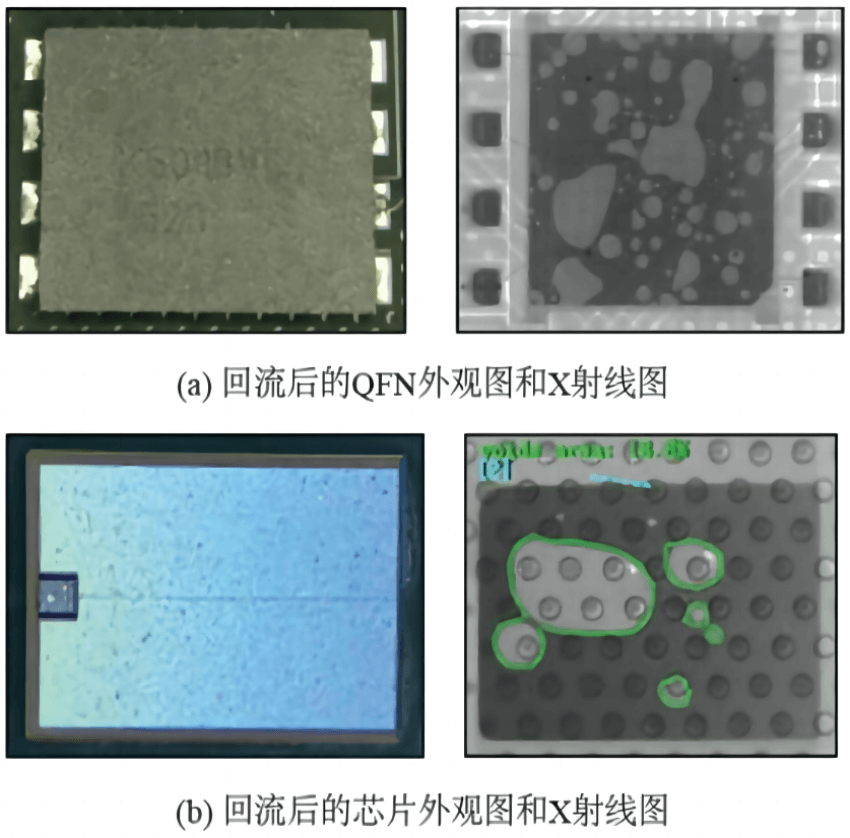
QFN و هولوگرام تراشه (اشعه ایکس)
از آنجایی که اندازه مهره قلع، ضخامت توری فولادی، سرعت سطح باز شدن، شکل شبکه فولادی، زمان برگشت و دمای پیک کوره همگی بر خلاهای جوشکاری جریان مجدد تأثیر میگذارند، عوامل مؤثر زیادی وجود دارد که مستقیماً با آزمایش DOE و تعداد آزمایشهای آزمایشی تأیید میشوند. گروه ها خیلی بزرگ خواهند بود. لازم است عوامل اصلی تأثیرگذار از طریق آزمون مقایسه همبستگی به سرعت غربالگری و تعیین شوند و سپس عوامل اصلی تأثیرگذار از طریق DOE بهینه سازی شوند.
3.1 ابعاد سوراخ های لحیم کاری و مهره های قلع خمیر لحیم کاری
با تست خمیر لحیم SAC305 type3 (اندازه مهره 25-45 میکرومتر)، سایر شرایط بدون تغییر باقی میمانند. پس از جریان مجدد، سوراخ های لایه لحیم اندازه گیری شده و با خمیر لحیم نوع 4 مقایسه می شود. مشخص شده است که سوراخ های لایه لحیم کاری بین دو نوع خمیر لحیم کاری تفاوت قابل توجهی ندارند، که نشان می دهد که خمیر لحیم کاری با اندازه مهره های مختلف تأثیر آشکاری بر سوراخ های لایه لحیم کاری ندارد، که یک عامل تأثیرگذار نیست. همانطور که در شکل نشان داده شده است. 6 همانطور که نشان داده شده است.
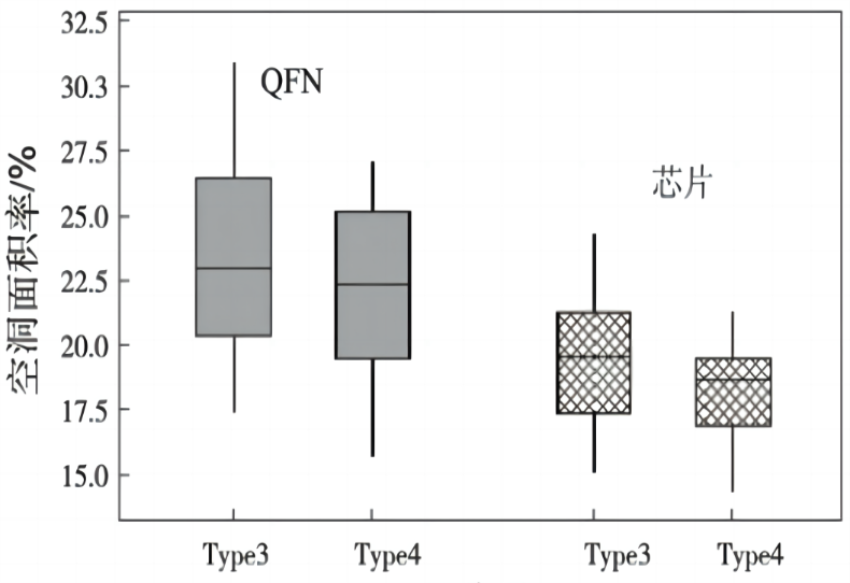
مقایسه سوراخهای پودر قلع فلزی با اندازههای مختلف ذرات
3.2 ضخامت حفره جوش و مش فولادی چاپ شده
پس از جریان مجدد، ناحیه حفره لایه جوش داده شده با مش فولادی چاپ شده با ضخامت های 50 میکرومتر، 100 میکرومتر و 125 میکرومتر اندازه گیری شد و سایر شرایط بدون تغییر باقی ماند. مشخص شد که اثر ضخامتهای مختلف مش فولادی (خمیر لحیم کاری) بر QFN با مش فولادی چاپ شده با ضخامت 75 میکرومتر مقایسه شد با افزایش ضخامت مش فولادی، سطح حفره به تدریج به آرامی کاهش مییابد. همانطور که در شکل 7 نشان داده شده است، پس از رسیدن به یک ضخامت معین (100μm)، ناحیه حفره معکوس شده و با افزایش ضخامت مش فولادی شروع به افزایش می کند.
این نشان میدهد که وقتی مقدار خمیر لحیم افزایش مییابد، قلع مایع با رفلاکس توسط تراشه پوشانده میشود و خروجی خروج هوای باقیمانده تنها از چهار طرف باریک است. هنگامی که مقدار خمیر لحیم تغییر می کند، خروجی هوای خروجی باقیمانده نیز افزایش می یابد و فوران هوای پیچیده شده در قلع مایع یا گاز فرار فرار قلع مایع باعث پاشیدن قلع مایع در اطراف QFN و تراشه می شود.
این آزمایش نشان داد که با افزایش ضخامت مش فولادی، ترکیدن حباب ناشی از خروج هوا یا گاز فرار نیز افزایش مییابد و احتمال پاشیدن قلع در اطراف QFN و تراشه نیز به ترتیب افزایش مییابد.
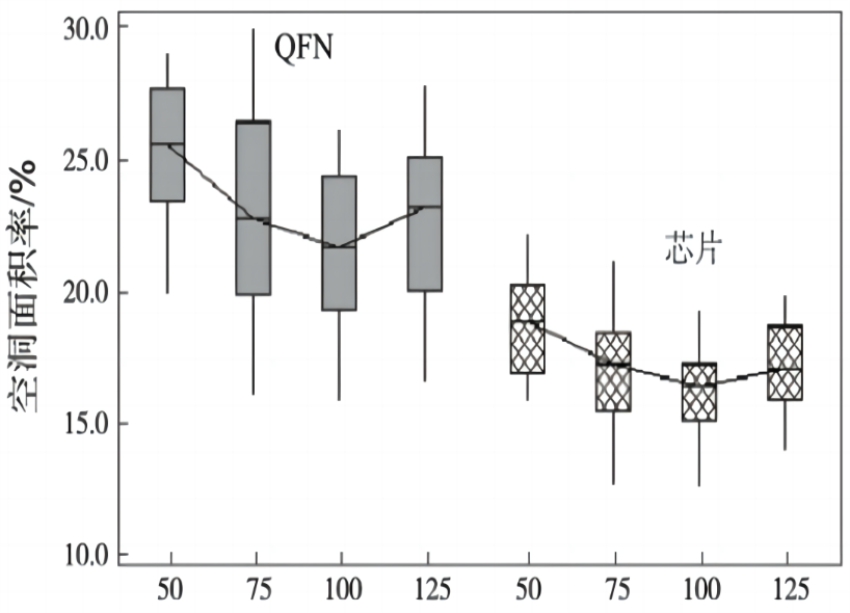
مقایسه سوراخهای مش فولادی با ضخامتهای مختلف
3.3 نسبت مساحت حفره جوش و دهانه مش فولادی
مش فولادی چاپ شده با نرخ باز شدن 100%، 90% و 80% تست شد و سایر شرایط بدون تغییر باقی ماند. پس از جریان مجدد، سطح حفره لایه جوش داده شده اندازه گیری و با توری فولادی چاپ شده با نرخ باز شدن 100٪ مقایسه شد. مشخص شد که تفاوت معنی داری در حفره لایه جوش داده شده در شرایط نرخ باز شدن 100% و 90% 80% همانطور که در شکل 8 نشان داده شده است وجود ندارد.
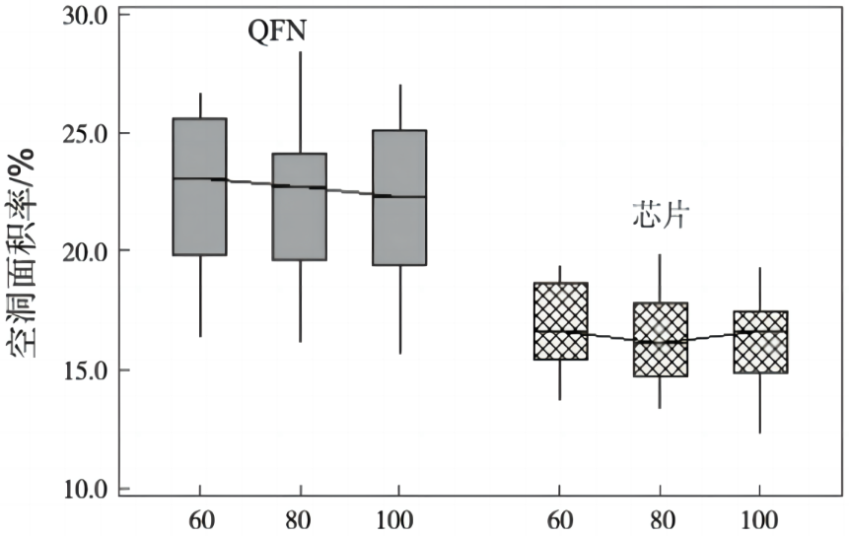
مقایسه حفره سطح بازهای مختلف مش های فولادی مختلف
3.4 حفره جوش داده شده و شکل مش فولادی چاپ شده
با آزمایش شکل چاپ خمیر لحیم کاری نوار b و شبکه شیبدار c، سایر شرایط بدون تغییر باقی می مانند. پس از جریان مجدد، ناحیه حفره لایه جوش اندازه گیری شده و با شکل چاپی شبکه a مقایسه می شود. مشخص شد که در حفره لایه جوش تحت شرایط شبکه، نوار و شبکه شیبدار، همانطور که در شکل 9 نشان داده شده است، تفاوت معنی داری وجود ندارد.
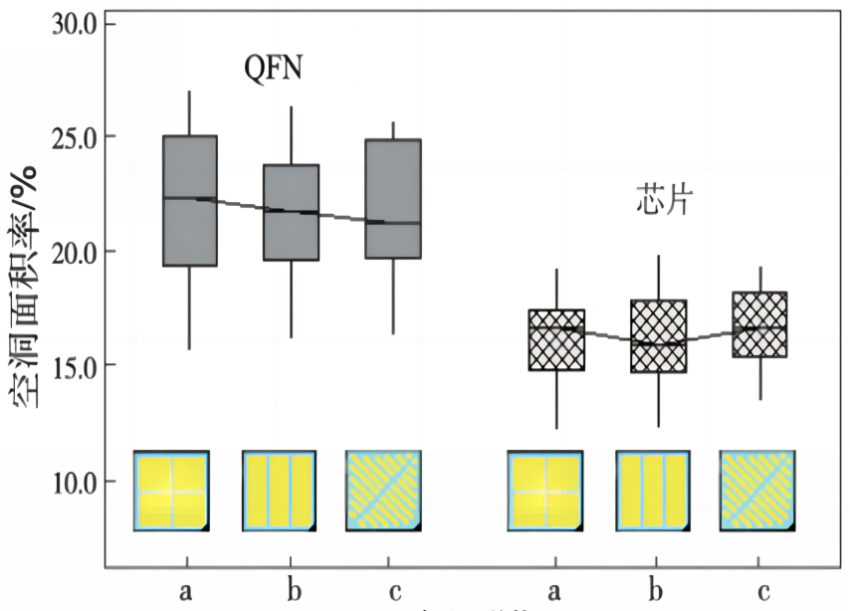
مقایسه سوراخ ها در حالت های مختلف باز شدن توری فولادی
3.5 حفره جوش و زمان رفلاکس
پس از تست ریفلاکس طولانی مدت (70 ثانیه، 80 ثانیه، 90 ثانیه)، سایر شرایط بدون تغییر باقی می مانند، سوراخ لایه جوش پس از رفلاکس اندازه گیری شد و در مقایسه با زمان رفلاکس 60 ثانیه، مشخص شد که با افزایش زمان رفلاکس، سطح سوراخ جوش کاهش یافت، اما دامنه کاهش به تدریج با افزایش زمان کاهش یافت، همانطور که در شکل 10 نشان داده شده است. در قلع مایع مذاب پیچیده شده است، اما پس از افزایش زمان رفلاکس به زمان معینی، هوای پیچیده شده در قلع مایع به سختی دوباره سرریز می شود. زمان رفلاکس یکی از عوامل موثر بر حفره جوش است.
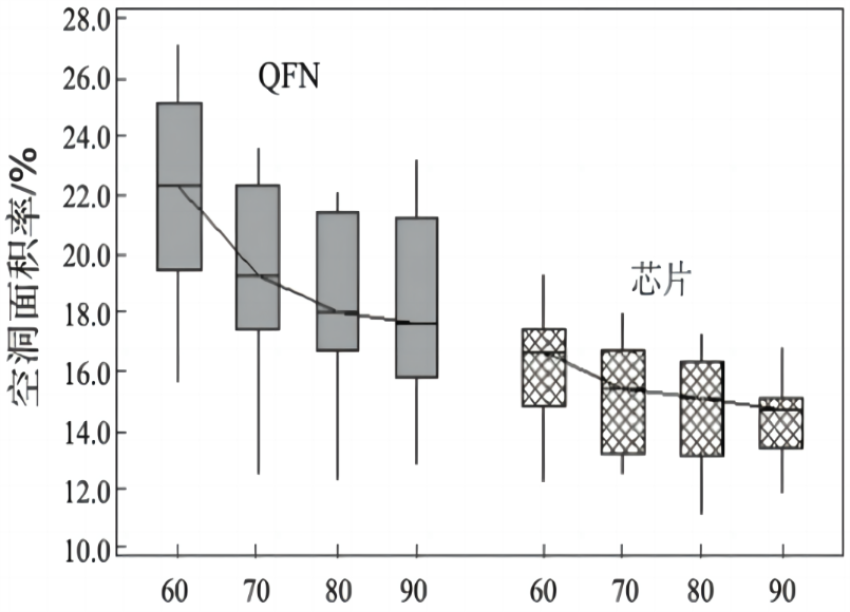
مقایسه بی اعتبار طول های مختلف رفلاکس
3.6 حفره جوش و دمای حداکثر کوره
با آزمایش دمای پیک کوره 240 ℃ و 250 ℃ و شرایط دیگر بدون تغییر، ناحیه حفره لایه جوش داده شده پس از جریان مجدد اندازه گیری شد و در مقایسه با دمای اوج کوره 260 ℃، مشخص شد که در شرایط مختلف دمای اوج کوره، حفره لایه جوش داده شده QFN و تراشه تغییر قابل توجهی نداشته است، همانطور که در شکل 11 نشان داده شده است. این نشان می دهد که دمای پیک مختلف کوره هیچ تاثیر آشکاری بر QFN و سوراخ در لایه جوش تراشه ندارد، که یک عامل تأثیرگذار نیست.
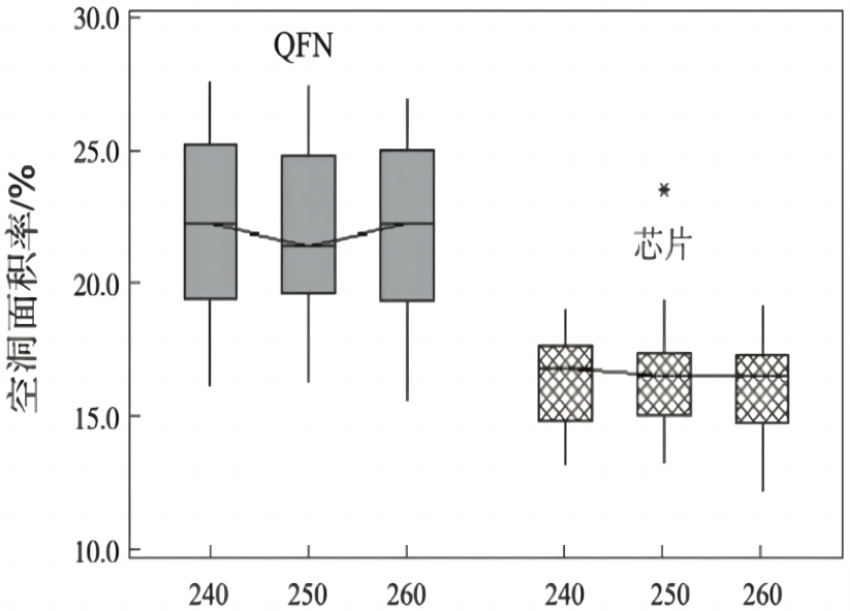
مقایسه بی اعتبار دماهای اوج مختلف
آزمایشهای فوق نشان میدهد که عوامل مهم مؤثر بر حفره لایه جوش QFN و تراشه زمان رفلاکس و ضخامت شبکه فولادی است.
4 بهبود حفره جوشکاری جریان مجدد چاپ خمیر لحیم کاری
4.1 تست DOE برای بهبود حفره جوش
سوراخ در لایه جوش QFN و تراشه با یافتن مقدار بهینه عوامل تأثیرگذار اصلی (زمان رفلاکس و ضخامت شبکه فولادی) بهبود یافت. خمیر لحیم کاری SAC305 type4 بود، شکل مش فولادی از نوع شبکه ای (درجه باز شدن 100٪)، دمای اوج کوره 260 ℃ بود و سایر شرایط آزمایش مانند شرایط تجهیزات آزمایش بود. آزمایش DOE و نتایج در جدول 3 نشان داده شده است. تأثیر ضخامت شبکه فولادی و زمان رفلاکس بر روی سوراخ های جوشکاری QFN و تراشه در شکل 12 نشان داده شده است. از طریق تجزیه و تحلیل برهمکنش عوامل تأثیرگذار اصلی، مشخص شده است که با استفاده از ضخامت مش فولادی 100 میکرومتر و زمان رفلاکس 80 ثانیه می تواند به طور قابل توجهی حفره جوشکاری QFN و تراشه را کاهش دهد. نرخ حفره جوش QFN از حداکثر 27.8٪ به 16.1٪ کاهش می یابد و نرخ حفره جوش تراشه از حداکثر 20.5٪ به 14.5٪ کاهش می یابد.
در آزمایش، 1000 محصول تحت شرایط بهینه (ضخامت شبکه فولادی 100 میکرومتر، زمان رفلاکس 80 ثانیه) تولید شد و نرخ حفره جوش 100 QFN و تراشه به طور تصادفی اندازهگیری شد. متوسط نرخ حفره جوش QFN 16.4٪ و متوسط نرخ حفره جوش تراشه 14.7٪ بود. نرخ حفره جوش تراشه و تراشه به وضوح کاهش می یابد.
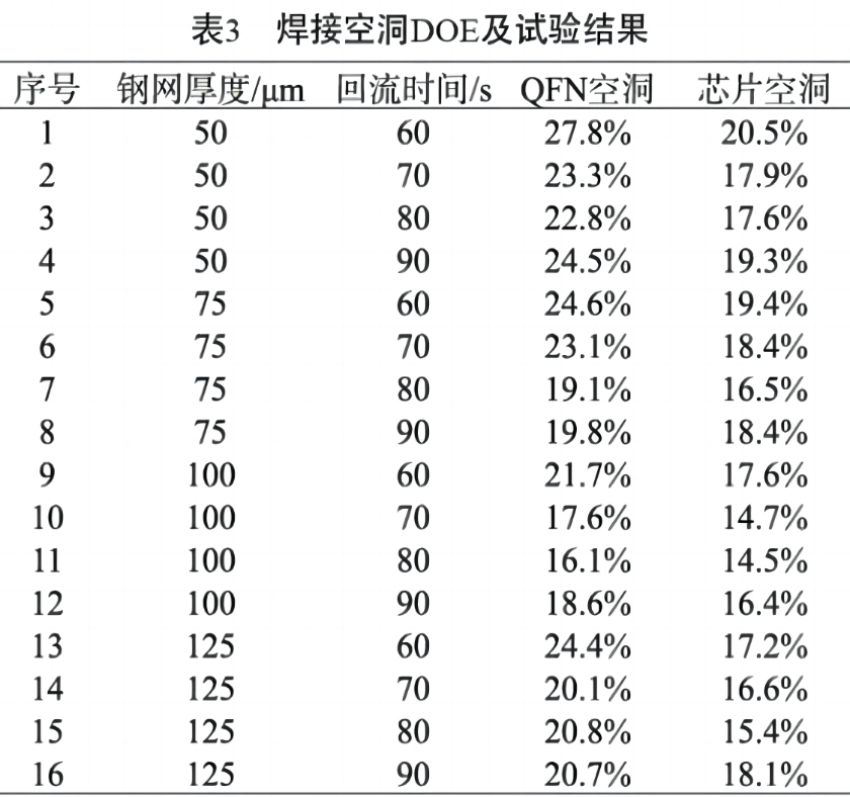
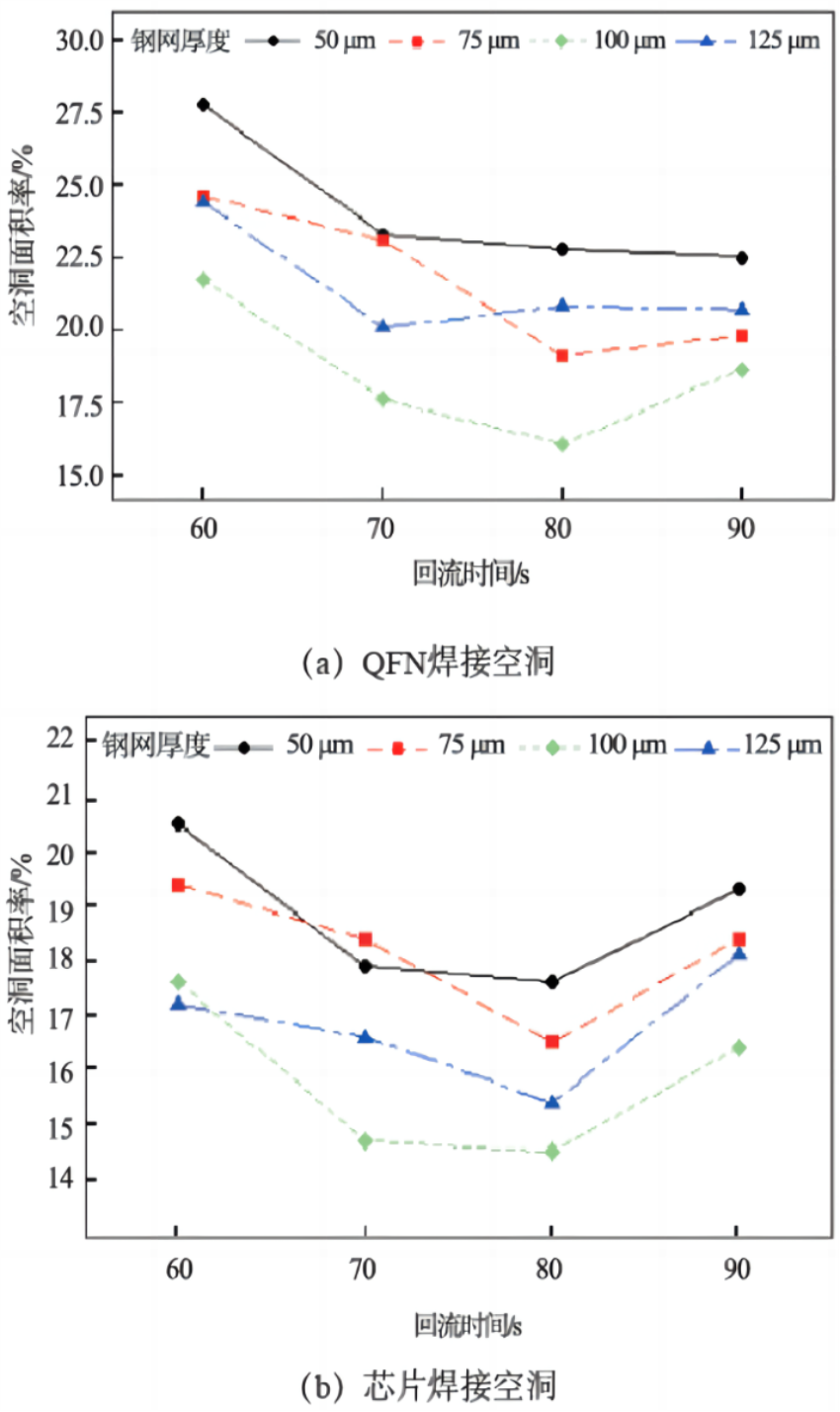
4.2 فرآیند جدید حفره جوش را بهبود می بخشد
وضعیت تولید و آزمایش واقعی نشان می دهد که وقتی ناحیه حفره جوش در پایین تراشه کمتر از 10٪ باشد، مشکل ترک خوردگی موقعیت حفره تراشه در طول اتصال و قالب گیری سرب رخ نخواهد داد. پارامترهای فرآیند بهینهسازی شده توسط DOE نمیتوانند الزامات تجزیه و تحلیل و حل سوراخها را در جوشکاری جریان مجدد خمیر لحیم کاری معمولی برآورده کنند، و نرخ ناحیه حفره جوش تراشه باید بیشتر کاهش یابد.
از آنجایی که تراشه پوشانده شده روی لحیم کاری از خروج گاز در لحیم کاری جلوگیری می کند، میزان سوراخ در پایین تراشه با حذف یا کاهش گاز پوشش داده شده لحیم بیشتر کاهش می یابد. فرآیند جدیدی از جوشکاری جریان مجدد با دو چاپ خمیر لحیم پذیرفته شده است: یک چاپ خمیر لحیم کاری، یک جریان مجدد که QFN را پوشش نمی دهد و تراشه خالی گاز را در لحیم تخلیه می کند. فرآیند خاص چاپ خمیر لحیم کاری ثانویه، پچ و رفلاکس ثانویه در شکل 13 نشان داده شده است.
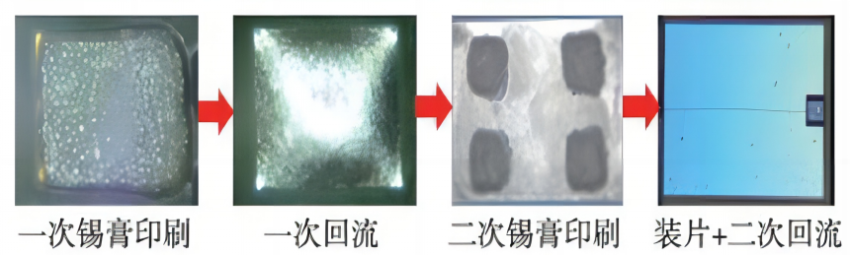
هنگامی که خمیر لحیم با ضخامت 75 میکرومتر برای اولین بار چاپ می شود، بیشتر گاز در لحیم کاری بدون پوشش تراشه از سطح خارج می شود و ضخامت پس از رفلاکس حدود 50 میکرومتر است. پس از اتمام رفلاکس اولیه، مربع های کوچکی بر روی سطح لحیم جامد سرد شده چاپ می شود (به منظور کاهش مقدار خمیر لحیم، کاهش میزان سرریز گاز، کاهش یا حذف پاشش لحیم کاری) و خمیر لحیم کاری با ضخامت 50 میکرومتر (نتایج تست بالا نشان می دهد که 100 میکرومتر بهترین است، بنابراین ضخامت چاپ ثانویه 100 میکرومتر است. 50 میکرومتر = 50 میکرومتر)، سپس تراشه را نصب کنید و سپس 80 ثانیه برگردانید. همانطور که در شکل 14 نشان داده شده است، تقریباً بعد از اولین چاپ و جریان مجدد هیچ سوراخی در لحیم وجود ندارد و خمیر لحیم در چاپ دوم کوچک است و سوراخ جوش کوچک است.
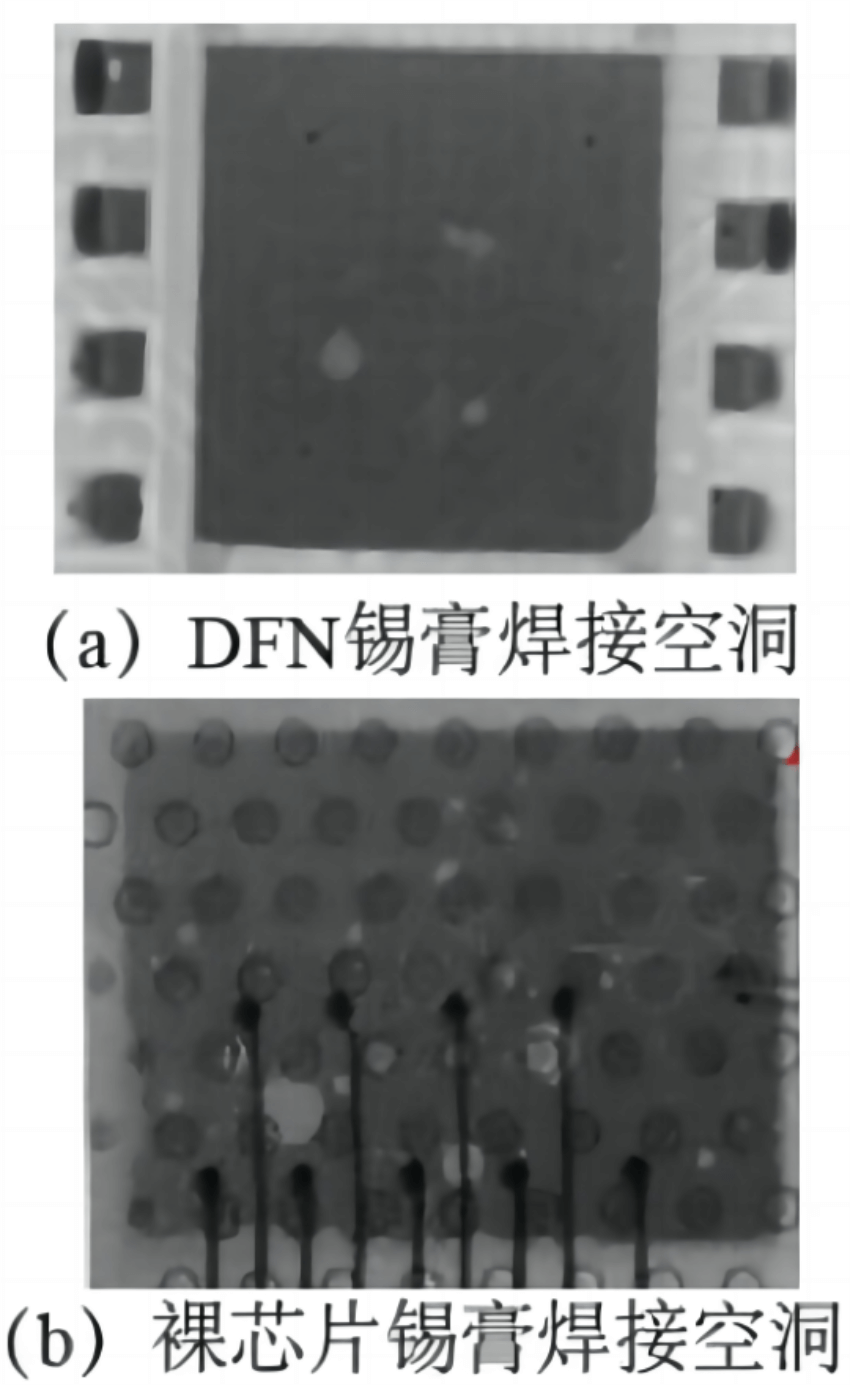
پس از دو چاپ از خمیر لحیم کاری، طراحی توخالی
4.3 بررسی اثر حفره جوش
تولید 2000 محصول (ضخامت توری فولادی چاپ اول 75 میکرومتر، ضخامت مش فولادی چاپ دوم 50 میکرومتر است)، سایر شرایط بدون تغییر، اندازه گیری تصادفی 500 QFN و نرخ حفره جوش تراشه، نشان داد که فرآیند جدید پس از رفلاکس اول بدون حفره، پس از رفلاکس دوم QFN حداکثر میزان حفره جوش 4.8٪ و حداکثر سرعت حفره جوش تراشه 4.1٪ است. در مقایسه با فرآیند جوشکاری چاپ تک خمیر اصلی و فرآیند بهینه سازی DOE، حفره جوش به طور قابل توجهی کاهش می یابد، همانطور که در شکل 15 نشان داده شده است.
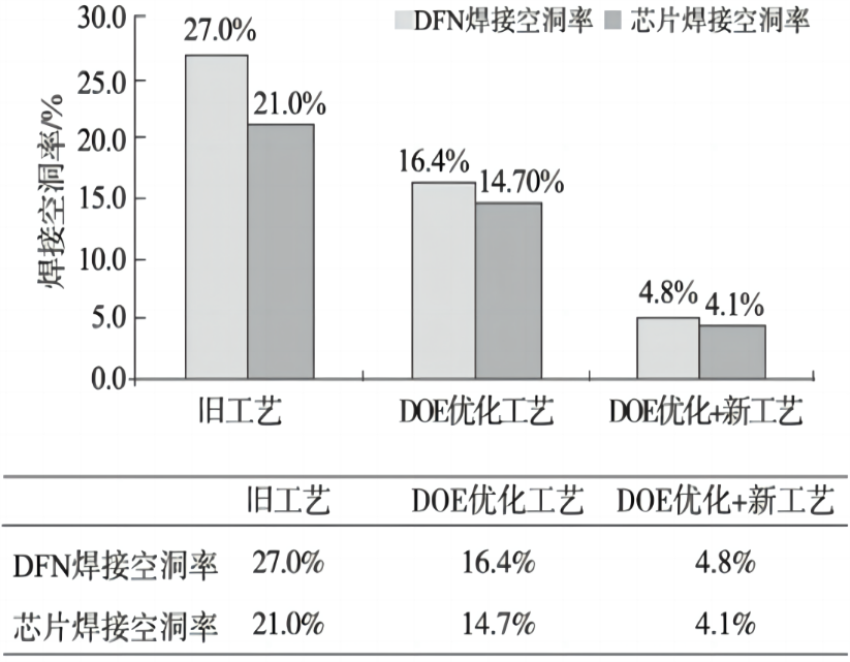
5 خلاصه
بهینه سازی مقدار چاپ خمیر لحیم کاری و زمان رفلاکس می تواند ناحیه حفره جوشکاری را کاهش دهد، اما میزان حفره جوش هنوز زیاد است. استفاده از دو روش جوشکاری مجدد با چاپ خمیر لحیم کاری می تواند به طور موثر و حداکثر سرعت حفره جوش را افزایش دهد. ناحیه جوش تراشه بدون مدار QFN می تواند در تولید انبوه به ترتیب 4.4mm x4.1mm و 3.0mm x2.3mm باشد. تحقیق در این مقاله یک مرجع مهم برای بهبود مشکل حفره جوشکاری سطح جوش بزرگ ارائه می دهد.